11 How Do You De-Risk Your Mine Plan?
So how do you de-risk a mine plan? There’s probably an entire book in discussing how you de-risk all of the components of a mine plan, this article will discuss just one component. The primary risk inherent in a mine plan is that it is wrong, in which case it is redundant. No mine should be making decisions based on a plan that is wrong or trying to execute it either.
A mine plan can be wrong when it is created, the primary causes being:
- Incorrect geological model or interpretation of it. There are many people significantly more qualified than me in this area and so it will not be discussed in this article.
- Errors within the underlying schedule such as numbers typed over formulae, incorrect naming or numbering of blocks, etc. This issue is easily resolved if the planner takes the time to carry out sufficient due diligence on the schedule before starting to plan with it. But unfortunately, planners often have insufficient time prior to scheduling to carry out proper due diligence.
- Use of the wrong assumptions in the plan. This is prevalent throughout the industry and by far the biggest culprit is the use of optimistic assumptions. It is generally driven from an executive level within the company and involves setting unrealistic schedule targets, or dictating assumptions are used that are higher than historical performance. Optimistic scheduling is a disease and deserving of its own set of articles as I believe it is the single largest cause of poor scheduling within the mining industry.
Or the mine plan becomes wrong at some time during the life of the plan. If there are no database errors in the plan, then it becomes wrong for one reason – variability. If you haven’t read any of my previous articles on variability, then I suggest starting with this article first. Variability happens across all components of the plan, from the scheduled quantities, to equipment productivities, to equipment operating hours.
If you want to de-risk a mine plan so that once created, it is more likely to be sufficiently correct to be useful, then you have two options:
- Decrease the variability in those elements which you have control over, which will reduce the spread of time taken for activities, reducing the probability of overlap between those activities.
- Introduce longer lag times between activities, this is the time between one activity finishing that block and the next activity having to start on that same block.
Let’s look at the relative impact those two changes have on a mine plan. To do this, we can use a simple example and the same tool that we used in Article 10. In this example, we are excavating a block of waste to uncover coal for mining (Block B). The coal mining fleet is excavating another block of coal (Block A), before relocating to mine Block B once it has been uncovered. Let’s assume the following:
- The variability of both activities is normally distributed.
- The waste excavator is planned to take 10 days to dig Block B and the variability in this activity is represented by a standard deviation that is 40% of the average, so a standard deviation of 4 days.
- The coal mining fleet is planned to finish the excavation of Block A 5 days after the waste excavator finishes Block B, so there is a lag between activities of 5 days.
- Coal mining of Block A is planned to take 6 days and the variability is represented by a standard deviation that is 40% of the average, so a standard deviation of 2.4 days.
Figure 1 shows the spread of potential finish times for the waste excavation activity and start times for the coal mining activity.
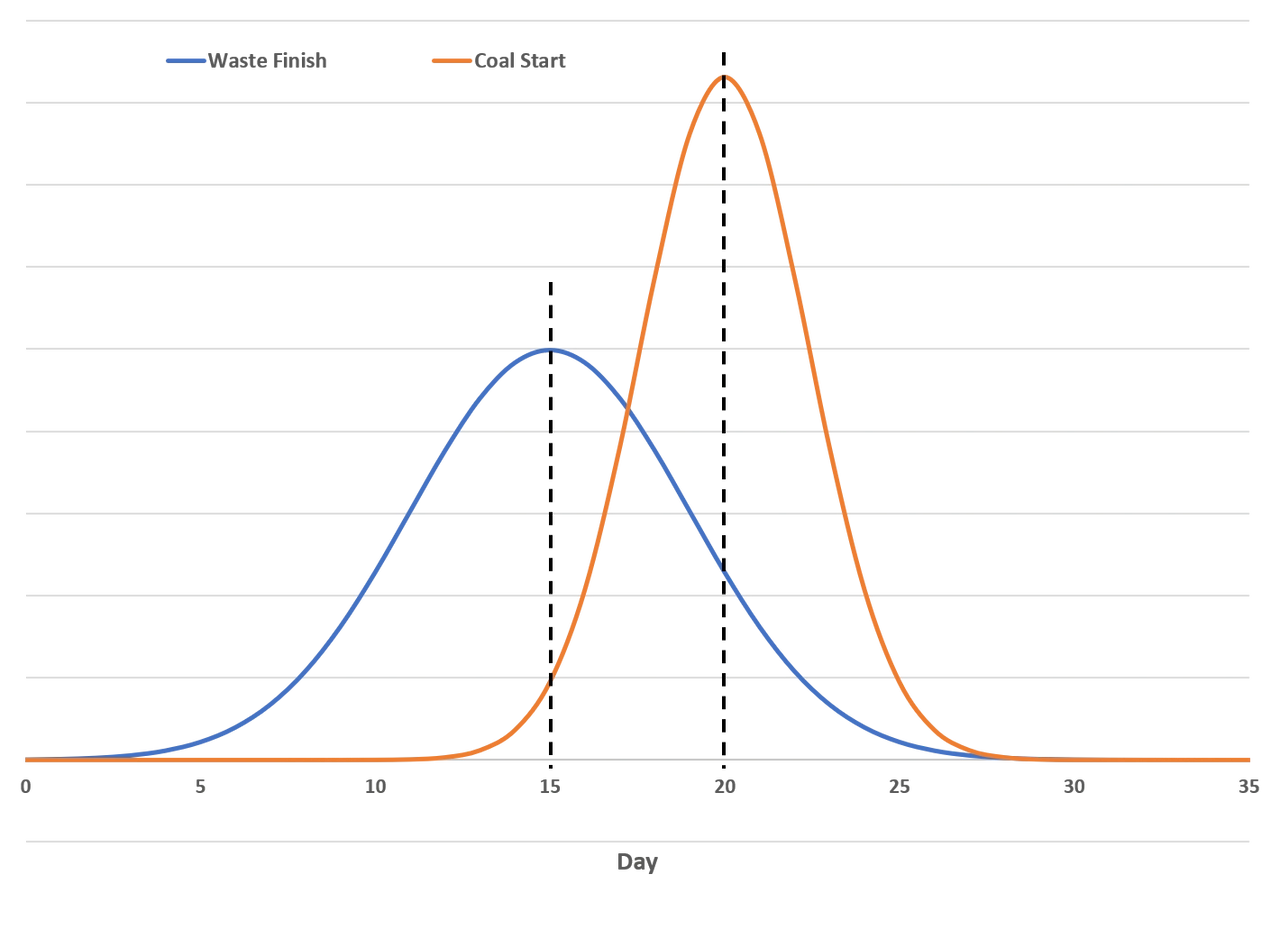
Figure 1 – Activity Interaction
As shown in Figure 2, this scenario leads to a 21% probability that there will be an overlap between the two activities, and consequently coal mining would be delayed by waste excavation.
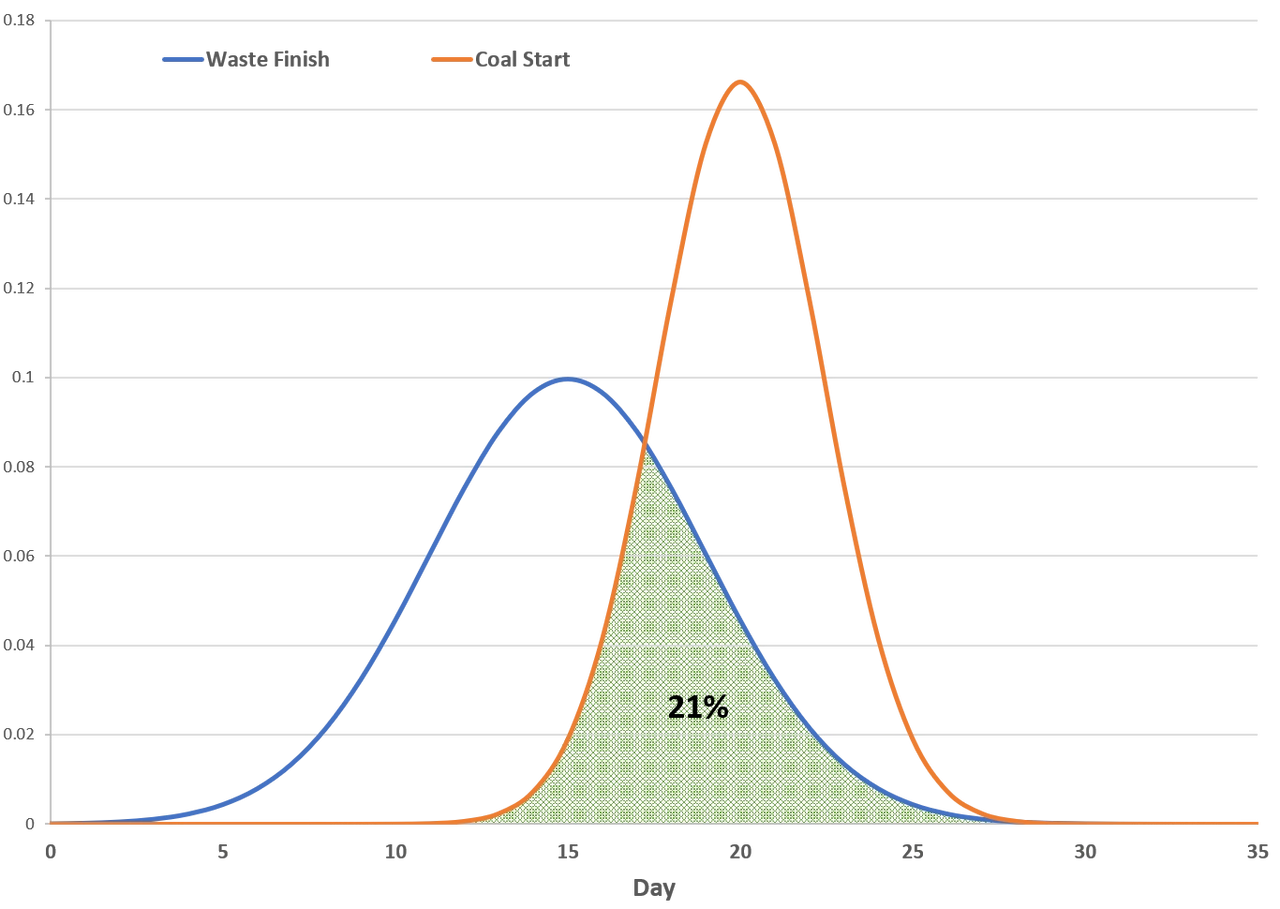
Figure 2 – Delay Probability
De-risking the plan involves reducing the probability of an overlap, as an overlap will result in either a re-sequencing of activities or coal mining being delayed. But either way, the mine is no longer operating at its maximum efficiency and the schedule is now wrong. To achieve this requires either an increase in inventories or a reduction in activity variability.
Let’s look at the impact of increasing inventories first, which in this scenario leads to an increase in the lag between activities. If we increase inventory by 30%, that would take the lag from 5 days to 6.5 days. As shown in Figure 3, this reduces the probability of an overlap from 21% to 14.7%.
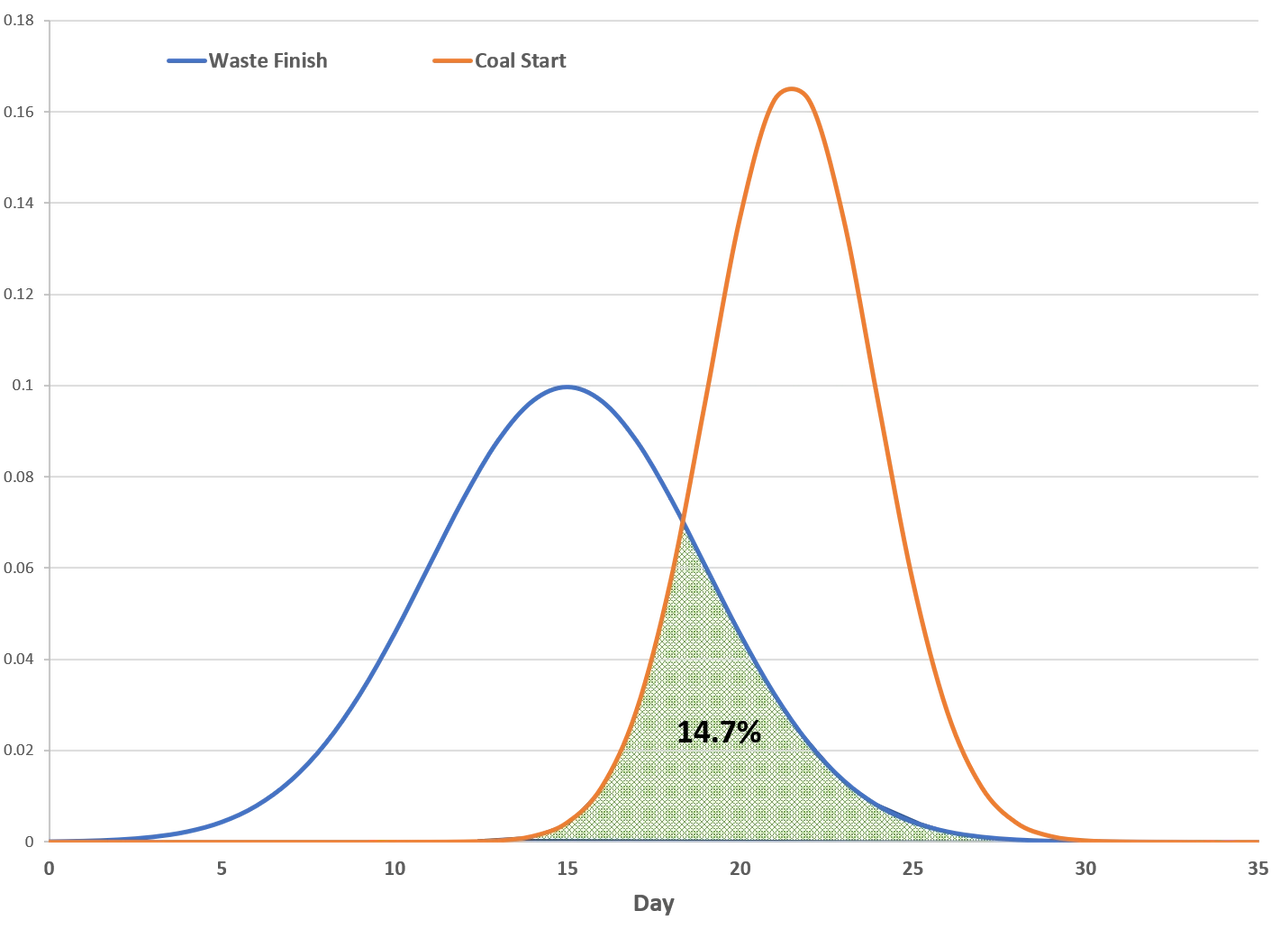
Figure 3 – Increased Inventory
Now let’s look at de-risking by reducing activity variability and use the same percentage change as that used in inventory change. So we have decreased the waste excavation standard deviation by 30% from 4 days to 2.8 days and for coal mining, the standard deviation has reduced from 2.4 days to 1.7 days. Figure 4 shows the impact on the probability of overlap, which has decreased from 21% to 12.5%. In this scenario, the probability of overlap is more sensitive to a reduction in variability, than it is to a change in lag. Although that may not be the case if the parameters were different, for example, significantly longer lags or reduced variabilities.
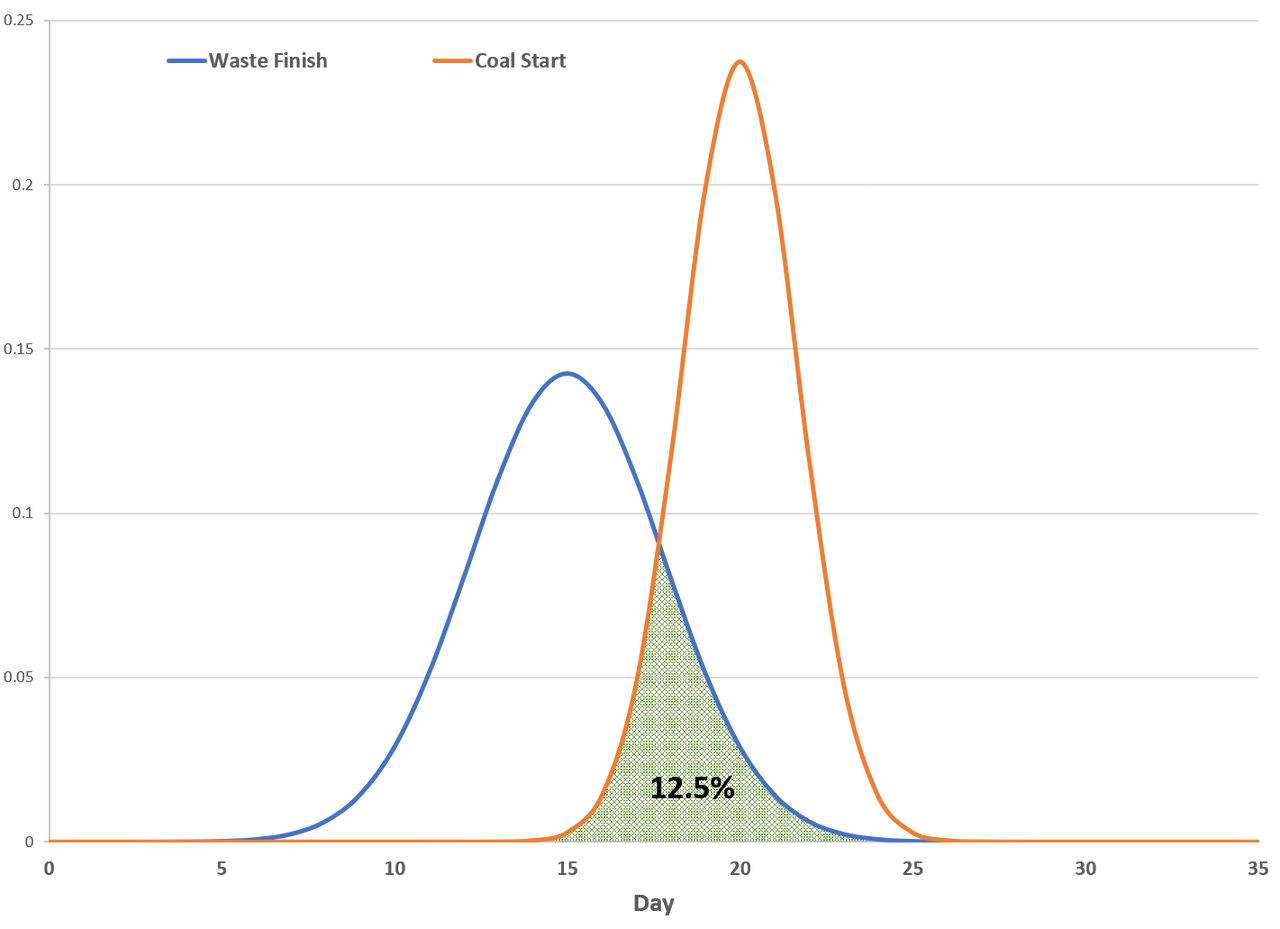
Figure 4 – Reduced Variability
Now let’s look at the financial impacts, starting with changes in inventory. Inventory is effectively cash spent earlier than it needs to be and the ongoing cost of that money spent early. The cost of debt at the moment is extremely low, however, for most mining companies the consideration is not the cost of borrowing. Mine sites always have a range of capital investment choices, such as purchasing new equipment, developing new mining areas, or debottlenecking processing plants. So money will only be invested in inventory growth if it has a better return on capital than those other investment opportunities. Obviously, that is extremely variable across mine sites, but for the sake of this example, let’s say that the minimum return on investment required is 40%. Let’s also assume truck and shovel excavation costs $4/bcm to dig, plus an additional $1/bcm to drill and blast, so a total cost of $5/bcm for the additional inventory.
If we assume that this mine has 5 diggers that are 600t sized diggers and each digger excavates 9 Mbcm per annum. This mine excavates 45Mbcm per annum of waste, which equates to 125,000bcm per day. If we want to increase the lag by 1.5 days, then we will need to excavate an additional 187,500bcm of waste at a total unit cost of $5/bcm. At a holding cost of 40%, this equates to an annual holding cost of $375,000.
For a mine excavating 45 Mbcm per annum of waste, that is not a huge cost in the scheme of their total budget, however, that is for only one activity and the mine will be carrying inventories for every activity. This is also just the cost of increasing truck/shovel waste by 1.5 days and so is not representative of the annual cost of the total inventory carried, which would be a large value for most mine sites.
But, let’s consider what it might cost to reduce variability. That is not a simple calculation, as reducing variability will require a systematic change process. But there is every likelihood it will conform to the 80/20 rule, where 80% of the reduction will come from tackling 20% of the issues that cause variability. Let’s take mine site culture for example, I’ve lost count of the number of mines that proudly report a ‘record shift’ when it happens and make a big deal out of it. But, they never talk about what the production was for the preceding or following shifts!
Boasting about record ‘one-off’ efforts only drives a culture of increasing variability and yet again highlights the complete lack of understanding that mining companies have of the impact of variation. Never yet have I heard a mine site boast of 10 shifts in a row with production between 13,000bcm per shift and 17,000bcm per shift!! Never yet have I ever seen a KPI which is a measure of a lack of variability. These are simple (and free) changes that would start a shift towards reducing variability, instead of increasing it.
So a mine site could spend $375,000 per annum on additional waste inventory, or it could start a systematic change process aimed at reducing variability, with many of these changes coming at no cost. I know which one I’d be doing………….
For other articles like this and quality conversations on a range of mining engineering subjects, I’d encourage you to join the LinkedIn Group called MinErs Digs, click here.