19 Drill & Blast Inventories – Are You Missing One?
For the mining industry, inventories play a critical role in allowing us to manage variability in our plans. In that scenario, then there is at least one additional inventory we should be managing – “Available To Drill” inventory. I haven’t come across it in use at any mine sites, but I believe at some it could prove to be essential to efficient operations.
Many mine sites measure and report against blasted inventory, or drilled inventory, or both. But is anyone completing the cycle by scheduling, measuring, and reporting “available to be drilled” inventory? At many mine sites, the drills do have lower utilisation rates and subsequently, excess drilling capacity (on a short-term basis) is often required to achieve annual drill metre requirements. Why? Because on many occasions, drills are parked up as a result of there being nowhere for them to drill!!!
It is the third piece of the pie that is missing. There are three steps to having sufficient quantity and quality broken stocks – having the right places to put the drills, drilling at an adequate rate and then blasting at an adequate rate. Across the three it is possible to determine a total inventory range that will ensure that a mine site maintains adequate broken stocks (blasted inventory). The three inventories can be combined on a stacked bar basis per digging unit, as shown in the example below, to provide an immediate picture of how things are going, where the current issues are and where the future issues may be coming.
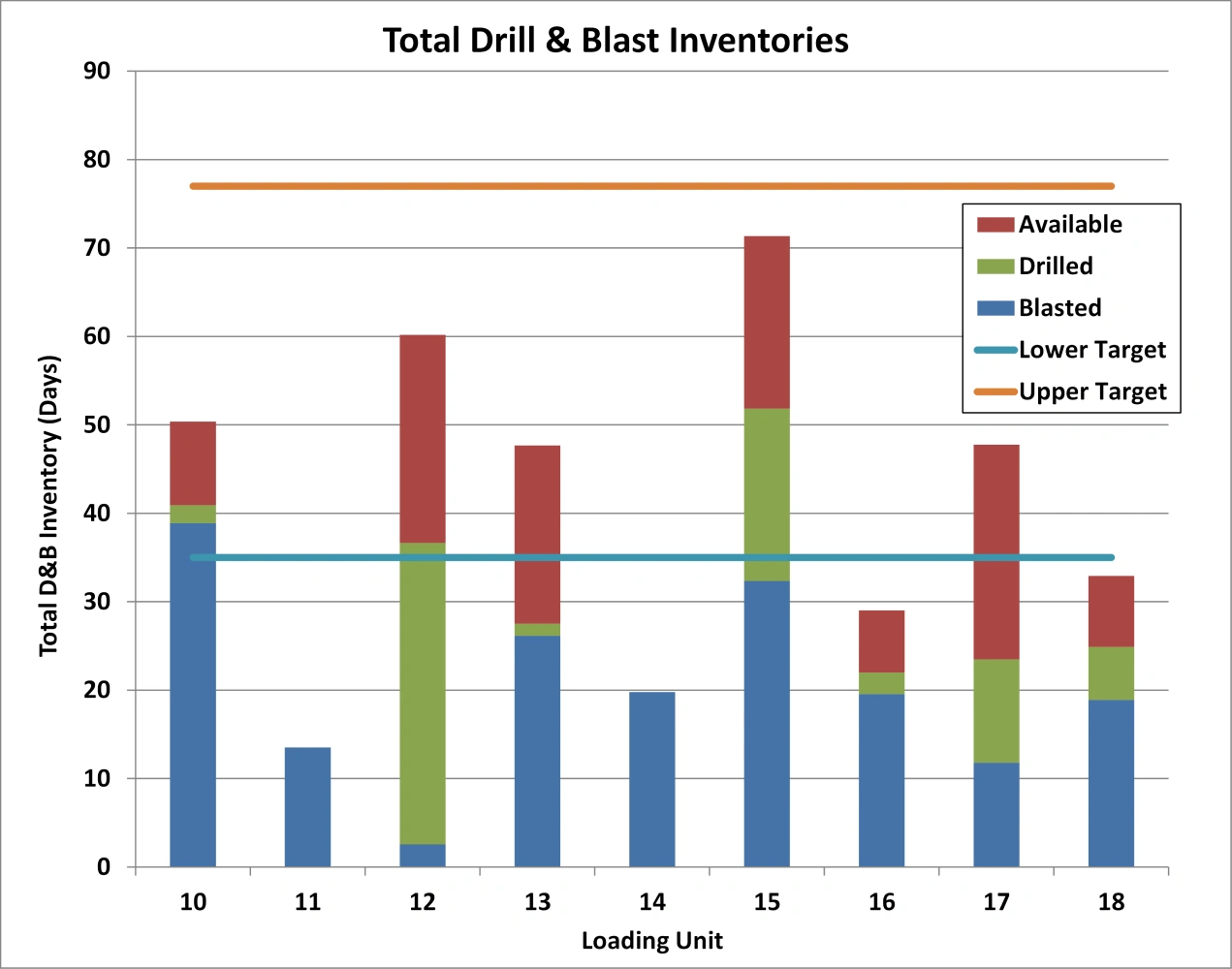
Immediate issues are where there are insufficient broken stocks, so Shovel 12 above has only about 3 days digging, that’s an immediate problem! However, it does have plenty of drilled and available to drill inventory though, so the longer term looks satisfactory. Shovel 11 on the other hand is a significant issue in the long term, it has 13 days of available dig material, but no drilled inventory and worse still, nowhere for the drill to even drill. So what is extremely beneficial in this process is that each inventory is an early indicator to the following inventory. For example, if the available to drill inventory is low, then unless the drilled inventory is very high, there will be an issue with drilled inventory in the future.
At mine sites where excavators move between mining areas regularly, this process could be carried out on a pit (or bench) basis instead. It will serve the same purpose.
The aim is that the regular use of the three inventories will highlight problem areas in time to see issues looming and regulate them. Who can argue that the earlier you see problems coming, the better that is for any mine site??